4-Face Flexible Solution at Sizewell B
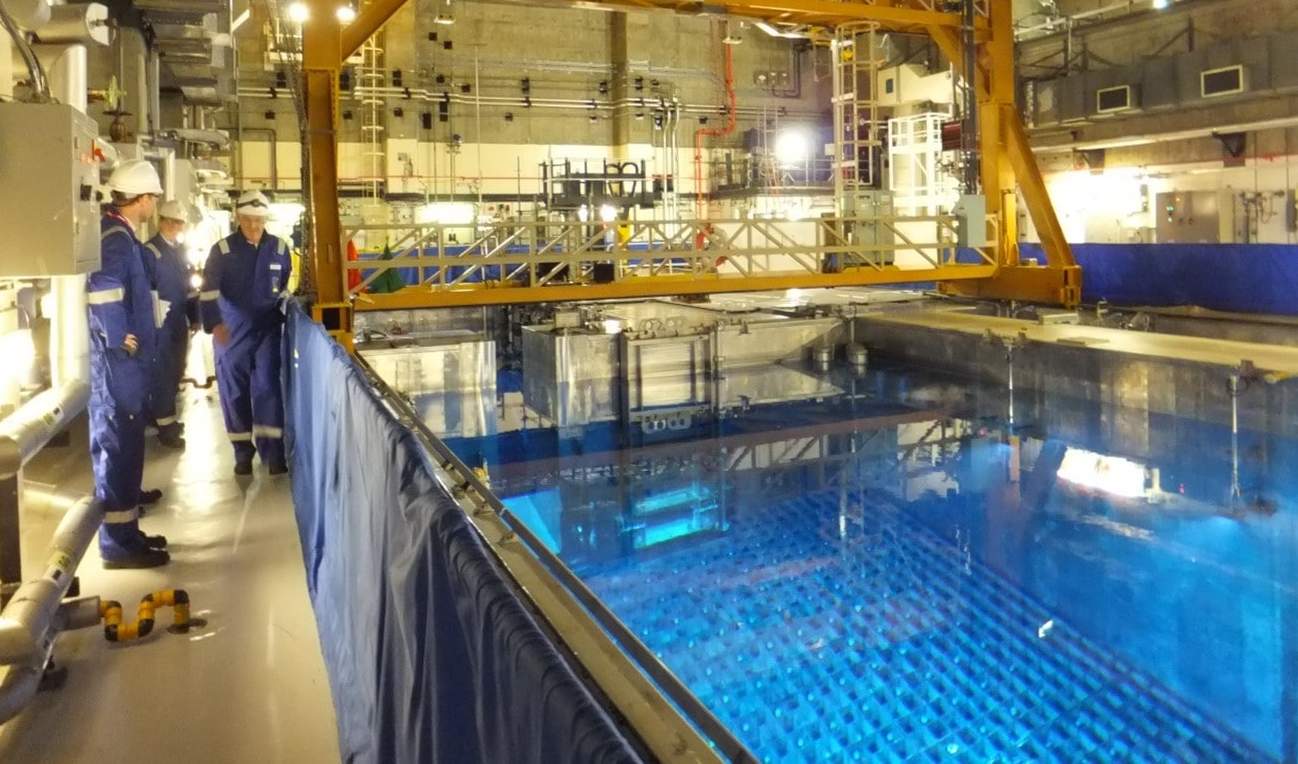
Background/Challenge
Sizewell B is a 1200 MW(e) PWR situated on the coast approximately two hours north-east of London, UK. The plant came into operation in 1995 and 20 years later the spent fuel storage was reaching max capacity. The original plan during construction of the reactor was to send spent fuel for reprocessing, but in 2015 no such route was available, so the plant opted for dry fuel storage. A dry fuel store is a method of storing used nuclear fuel that has already been cooled in the used fuel pond. The fuel is loaded into a metal canister which is then welded shut. This is then placed in a large, leak-tight steel and concrete cask. A dry fuel storage building is built next to the plant which houses these casks.
Before loading the spent fuel assemblies into the metal canisters, the plant must perform a thorough inspection of them; only fuel assemblies with perfect integrity are allowed to be stored in the canisters. Therefore, Sizewell B needed a system that could inspect all sides of the fuel assemblies to check fuel rods and spacer grids as well as bottom nozzles.
Sizewell B approached Ahlberg Cameras to present suitable cameras for the task and also create a solution for adjusting camera settings, recording inspections and more from multiple locations.
Our Approach
After discussion with engineers at Sizewell B, Ahlberg Cameras developed a solution that was given the name “4-Face Flexible Solution” which consisted of the following parts:
– 4-Face Camera System
For the 4-face camera system, a four-sided frame is designed and equipped with four highly radiation tolerant HD cameras, one on each side of the frame. Four radiation tolerant lights are also mounted on the frame, one in each corner. The 4-face frame is put in place over the up-ender in the fuel transfer canal. The camera and lighting cables are connected to a data recording system from which functions like pan, zoom and lighting can be adjusted.
– 5th Camera
A fifth camera is placed on a pole system situated in the area between the fuel transfer canal and the closest fuel storage rack. The camera cable is also connected to the data recording system. The fifth camera is used to see the bottom nozzle of the fuel assemblies.
– Remote Camera System
A sixth radiation tolerant HD camera is placed on a pole system which is attached to the railing on the Pond Fuel Handling Machine, PFHM. The camera is controlled by a remote connected to a camera control unit which is mounted in a rack on the PFHM. An adjacent video monitor provides a live view of the camera image.
– Data Recording System
A 19” rack is placed on the fuel building floor next to the up-ender position. A monitor provides the operator with views from the 4-face camera system (providing video from each side of the fuel), the 5th camera (providing video from the bottom nozzle), or from the remote camera system. The 4-face operations can be controlled from either the data recording system or the remote camera system.
Sizewell requested the flexibility of controlling the complete system either from the data recording system close to the up-ender, or from the remote camera system placed on the Pond Fuel Handling Machine. This required data connection between the data recording system and the PFHM. Fiber optics were installed to connect these two points, partially in drag chain.
Redesigning a standard 4-face solution with the possibility to operate it remotely from the PFHM allowed Sizewell greater functionality with the same low number of operating staff. Different parts of the system can be used separately or for other tasks. For example, by using the 4-face camera system during a regular offload to find failed fuel allows the plant personnel extra time during an outage to reconsider placement of possible affected fuel assemblies.